BMW M135i - Gyeon All Surface Treatment
- Aaron Brooks
- Oct 23, 2016
- 10 min read
Hot hatchbacks are loved by all generations for their cheap to repair costs and with the ability to perform on a track day as comfortably as they do heading to the supermarket they're the perfect choice for anyone. Due to the market of hot hatchbacks is of course based around taking an ordinary day-to-day little car and adding a larger engine, upgraded suspension and possibly a few creature comforts removed in the pursuit to save weight, the market is as near as makes no difference a front wheel drive haven. Petrol heads often speak of rear wheel drive being the choice to have, although with this layout being more commonly found in more expensive coupes, sports and convertible vehicles the additional cost to purchase (and maintain) them often doesn't become feasible for some meaning that the only option to have their fun would be a FWD little hatch - until BMW launched their 1 Series. Featuring a front engine, rear wheel drive layout in a short chassis made the BMW 1 Series an affordable way to have fun without the burdens of vehicle size, maintenance costs and, if we're being honest, lack of in car equipment in most hot hatches. BMW eventually moved the 1 Series from an ordinary hatchback with a great drive layout into a great hot hatchback with a great drive layout with their M135i model. A 326bhp powerhouse located under the bonnet puts the BMW M135i into similar power ranges as the earlier 1M coupe that featured a 3.0litre twin-turbo straight six engine, the M135i only having a single turbo. Additional 'M' bolt ons, tuning options and spec certainly make the M135i a serious choice for anyone looking for a small car but want the performance of something much larger and prestigious.
The BMW M135i we were presented with was purchased by an existing client of ourown, after receiving a similar service with other market brands previously he said it was a 'no-brain' decision to get his latest investment detailed also. So, lets get to work.. The M135i was delivered to us in a reasonable condition with little road soiling and only a few spattering of what seemed to be mud splashes. Looking further, it was evident that the BMW had never been decontaminated due to the heavy build up of metal fallout present (to come later)...






To begin the detail, the BMW was raised onto chassis supports in order to remove the alloy wheels and gain access to rear spokes and inner arches. Even though we use wheel woollies in our regular wheel cleaning process they are often limited in accessing every part of the rear-spokes - much like these wheels, there is often a slight dip where the manufacture markings are stamped, a woollie would simply clean the highest surfaces and leave the lower parts untouched. A Gyeon Q2RIM application requires the wheel be as clean as possible for best durability and finish, for this we removed the wheels. Auto Finesse Imperial wheel cleaner was used to remove the surface build up of brake dust and soiling whilst an all-purpose cleaner (APC) was used to scrub the tyre side walls using a stiff bristle tyre brush. Once rinsed, any tar spotting was removed from the wheels using Gyeon Q2MTAR prior to any remaining brake dust was removed by soaking the wheels in Gyeon Q2MIRON for 5-6 minutes. Any remaining metal particles would be highlighted by a chemical reaction where the product would turn a deep shade of purple, this is caused by a chemical reaction in which the Q2MIRON turns the firstly stubborn particles into a water soluble state. As the design of the wheels were a little unusual with a groove located between the wheel barrel and the rear of the spokes, anyone without suitable tooling would find it difficult to access this area causing the brake dust to build up and become increasingly difficult to remove. This grooved area needed another two/three application of Q2MIRON to remove the build up, agitating each application after a few minutes of it being left to soak...




Whilst the wheels were left to soak, the under arch areas were sprayed with an APC and a long-reach brush worked the product to remove a surface build up of road soiling. Plastic arch liner sections, fabric arch liners and exposed painted chassis were all agitated to ensure a good cleanse in all areas. A stiff bristled engine/wheel brush was used to free dirt from mounting crevasses, clips and fixing surrounds and other harder to reach areas. A solvent tar removing agent was then sprayed liberally into the arches in order to soften tar deposits prior to using a brush and microfiber cloth to remove as much tar as possible. A thorough pressure rinse then carried away all lifted dirt to reveal an under-arch area that resembled that of the day it was purchased. The brake calipers were misted with Auto Finesse Imperial and agitated thoroughly with a boars hair detailing brush to remove brake dust..






Once the arches and wheels were cleaned and rinsed thoroughly, the wheels were re-fitted to the BMW and it was then lowered off the chassis supports to continue with the body cleansing. The under bonnet area was more than presentable with little build up, only a light surface dust covering was present that a light brush over with a little APC sorted easily. The scuttle panel was also agitated to clean away any dirt before Gyeon Q2TRIM would be installed later in the detail. A rinse with a pressure washer and the bonnet was closed once again. A layer of Gyeon Q2MFOAM was blanketed over the entire car and left to dwell for approximately six minutes whilst we filled our buckets with Auto Finesse Lather shampoo..



Once the foam was rinsed away thoroughly with a pressure washer intricate areas such as grills, badges and window seals were sprayed with an APC and a boars hair detailing brush worked into the crevasses. The BMW was then carefully washed with the two bucket method and a synthetic deep-pile wash mitt to remove any remaining road soiling that the pre-wash stage couldn't remove without a physical wash. Working from top to bottom, the BMW was washed in straight lines and as little pressure as possible until each panel was completed one-by-one. A thorough pressure rinse was then carried away lifted soiling with clean water. The first decontamination step would be to remove the tar deposits using a dedicated tar remover. Applying the product onto the panel allowed any minor spots to be removed and larger spots to 'run' as the product began to dissolve it. A gentle wipe with a microfiber pre-sprayed with tar remover aided in removing and collecting any excess tar remover and tar deposits. Stubborn tar spots were re-treated in the same way until removed entirely. Once again the treated panels were rinsed free of any remaining tar remover. Auto Finesse Iron Out was then liberally sprayed over the entire car and left to dwell in which time any metal particles present would be highlighted with a transformation from clear to deep purple. This particular vehicle was showing high levels of fallout, especially on the rear panels..




After leaving the Iron Out to dwell for around 6-8 minutes, the car was thoroughly rinsed with a pressure washer ensuring that areas that the product can collect were given extra attention. A further inspection of the paintwork around the areas that showed the most fallout contamination showed evidence of some remaining contamination. Some very small black specs of residual fallout were visible. The entire vehicle was then taken into the third stage stage of decontamination where a surface preparation towel would physically remove any remaining contamination - the previous two steps are considered to be the chemical decontamination processed due to them requiring no physical input for them to perform (even though it does aid them). Each panel was carefully massaged with the surface preparation towel (claybar alternative) using a soapy water solution as lubrication, the polymerized rubber coating on the towel acting as an abrasive to remove any remaining contamination including over spray. The car was re-covered in a layer of Gyeon Q2MFOAM to work any remaining tar and fallout remover residues from water traps and collection areas whilst simultaneously carrying away all lifted contamination without the need to re-wash the car. The foam was left for only a fe minutes this time round, as there was no need for the foam to act as a cleaner the dilution was lessened and the time to dwell was reduced - this second foaming was purely to carry away any remains that had already been lifted...


With the wash and decontamination processes now completed, the BMW was moved inside and dried off using a combination of drying towels and warm filtered air to ensure grills, badges and other areas weren't holding any water to become an annoyance later in the service. Now dried off and moved into the working area, the wheels were once again removed and the M135i was then inspected for defects such as bird etching and other surface staining. The owner also pointed out and requested we give a little more attention to the black pillar trims that were evidently swirled and damaged. The pillars and bird etchings were polished with a cutting polish on a polishing pad to remove the damage prior to the entire vehicle undergoing a single stage polish with an ultra-fine finishing polish..





After the pillar trims and the area of bird etching were taken care of, the entire car was then machine polished with an ultra-fine finishing polish in order to increase the overall gloss levels and prepare the paintwork for its ceramic coating application. As the paintwork was white, the appearance of swirls and marks is far less than that of a black, with this in mind the owners main priority for this service was to get the car looking great and protected from top to bottom rather than to achieve a certain correction level. The polishing was completed and all areas to be treated were de-greased and removed of any remaining polishing oils and residues with Gyeon Q2MPREP; whilst IPA has the ability to remove polishing oils, a dedicated panel wipe (such as Gyeon Q2MPREP) is a far more effective choice prior to a coating being installed.

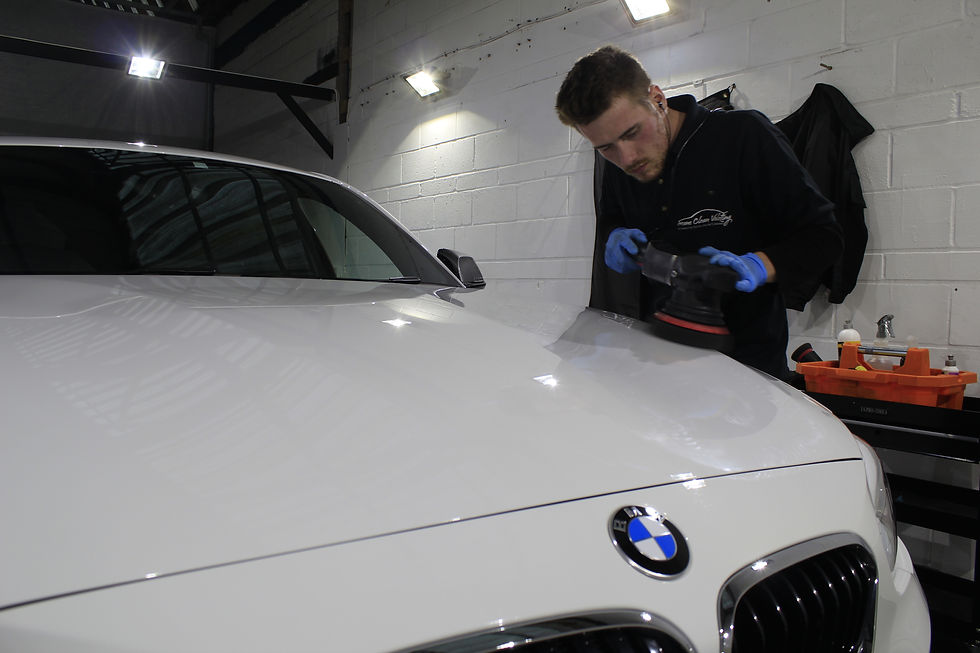
With the paintwork prepared and cleared of residues, two layers of Gyeon Q2MOHS were applied to all exterior paint. Applying panel-by-panel (larger panels were split into sections), the product was spread and then two brand new microfiber towels were used to remove the residue. The first acting as a 'spreading' towel and the second then buffing the remainder of the product until a smear free glossy finish was produced. A one hour window was given between the final panel being coated with the first layer of Q2MOHS and the beginning of the second layer. This second layer was worked in the same manor as the first. Ensuring all product residue is essential when applying a coating as once they begin to cure they begin to harden into an almost glass-like form which become difficult to remove when installed incorrectly. The exterior glass was removed of any surface spotting using Gyeon CLEANSE glass cleansing paste in overlapping circular motions until all the surface had been cleaned. A damp cloth then removed the CLEANSE residue and the glass was buffed until all smears had been removed. The glass was left to dry completely before Gyeon Q2REPEL was worked onto all glass surfaces, once again in overlapping circular motions. Two layers were applied to ensure the best coverage and durability of the product to achieve the desired 12+ months of clear vision, even in the harshest driving conditions. Any residue was once again buffed away until the glass was smear free. The body and glass surfaces were then force cured under infrared, this method aids in the coatings providing a durability that can match or even excel the expected lifespan of each. Force curing the coatings also reduces the cure time from twenty four hours to ten minutes per panel/section - this means that when time constraints are in place the vehicle can be used the same day as the coating are applied. During the time of curing the upper panels, the time was used to apply Gyeon Q2TRIM to exterior plastic and arch liners. Lower bumper grills were protected ensuring all tight areas received an application of the product with detailing swabs before a clean microfiber removed any excess product for an even finish. The Q2TRIM can also be force cured under infrared to extend life expectancy and prevent the plastics dulling or fading with UV damage.





The wheels were misted with Gyeon Q2MPREP and buffed to ensure the wheel surface was clean and free from dust to allow maximum adhesion of the Gyeon Q2RIM. A single layer was applied to both wheel faces and barrels ensuring all residue was buffed away using a sun gun alternative to see all areas as best as possible. The tyres were then dressed and protected with Gyeon Q2MTIRE to finalize the wheels protection. A single coat of Q2RIM was also applied to the brake calipers for ease of future cleansing..




As the wheels were coated a day previous to the body and glass, there was no need to force cure the wheels as the time between the application of the Q2RIM and the vehicles departure was over twenty four hours - the minimum time required to naturally cure the coating. A few of the wheel center caps were noticed to be a little off center. A simple removal of the caps and re-fitting them inline with the 'm' emblems found on a single spoke neatened things up a little..


The machine finished wheel hubs were also looking a little tarnished with no sign of previous maintenance. Auto Finesse Mercury metal polish and a fine wire wool was used to cleanse the surface to restore a brightened finish. The wheels were then re-fitted to the BMW whilst the force curing was continuing on the body..




Once the force curing had completed all panels of the M135i the final step of the Gyeon Q2MOHS application would be to apply Gyeon Q2MCURE. This is Gyeon's topcoat for any of their coatings and will act as a sacrificial layer whilst the Q2MOHS fully hardens over the next seven full days, preventing any waterspots damaging or effecting the performance of the coating. The engine compartment was misted lightly with Auto Finesse Dressle and left to dwell for a few minutes before excess was wiped away with a clean microfiber. Door window surrounds were dresses and protected with Gtechniq T1 Tyre&Trim for its rubber preserving properties before the gloss black exhaust tips were carefully removed of emission build up. A very light vacuum of all interior surfaces and a clean of the glass completed the turn around on this little BMW M135i. Ready to face all weather conditions for the next 18 months minimum thanks to our Gyeon All Surface Treatment.


















Comments